BALL VALVE
What is Stainless Steel Floating Ball Valve?
A stainless steel floating ball valve is a type of valve that utilizes a floating ball mechanism and is constructed primarily using stainless steel material.
The term “floating ball” refers to the design of the valve, where the ball inside the valve chamber is not fixed or attached to the stem. Instead, it is free to move or float within the valve body. The floating ball valve relies on fluid pressure to create a seal when the valve is closed. The pressure pushes the ball against the seat rings or sealing surfaces, ensuring a tight closure and preventing fluid flow.
Stainless steel is the chosen material for the construction of these valves due to its corrosion-resistant properties. Stainless steel alloys contain a significant amount of chromium, which provides excellent resistance to rust, corrosion, and staining. This makes stainless steel floating ball valves highly suitable for applications where fluids are corrosive or subjected to high temperatures.
Stainless steel floating ball valves find widespread use in various industries, including oil and gas, chemical processing, water treatment, and industrial processes. They are favored for their durability, resistance to corrosion, and compatibility with different fluids and operating conditions.
These valves are available in different sizes, pressure ratings, and connection types to accommodate diverse application requirements. They are known for their reliability, extended lifespan, and ability to withstand harsh environments. Stainless steel floating ball valves are particularly preferred in applications where fluid purity, hygiene, or resistance to corrosion is of utmost importance.
When the handle or lever is turned to align the hole in the ball with the flow direction, the valve is in the open position, allowing fluid to pass through. Conversely, when the handle or lever is rotated to block the hole, the valve is closed, preventing fluid flow.
Ball valves are commonly used in various industries and applications, including water and wastewater systems, oil and gas pipelines, chemical processing plants, power generation, and many others. They are valued for their durability, reliability, and ability to provide tight shut-off, making them suitable for both on/off and throttling applications. Additionally, ball valves offer low resistance to flow and are relatively easy to operate.
Advantages of STAINLESS STEEL BALL VALVE
Drop
A more powerful pump is not necessary for the movement of fluid and gas. This implies that there's a minimal pressure transition from high to low, which assures the seamless operation of the pipe components.
Stem
The valve design doesn't incorporate a stem component that shifts up or down with motion. As a result, no fluid or gas escapes the pipeline when the valve is activated or deactivated.
Easy to Operate
Stainless steel ball valves typically have a simple operation, often just a 90-degree turn, making them easy to open and close quickly.
Cost-Effective
Although the upfront cost may be higher than other materials, the long-term savings from reduced maintenance and longer lifespan make stainless steel ball valves a cost-effective choice.
Ball Valves By Body structure
One-Piece Ball Valve (1PC)
The body is formed from a single body piece in a one-piece ball valve. The ball is permanently fixed within the valve body, and the ends are threaded or welded. One-piece ball valves are compact and cost-effective, commonly used in applications with lower pressure and smaller sizes.

Two-Piece Ball Valve (2PC)
This type of ball valve consists of two separate pieces connected with thread or bolts. The body is divided into two halves, allowing easy access to the internal components, including the ball and seats. Two-piece ball valves are commonly used in applications requiring regular maintenance or inspection.
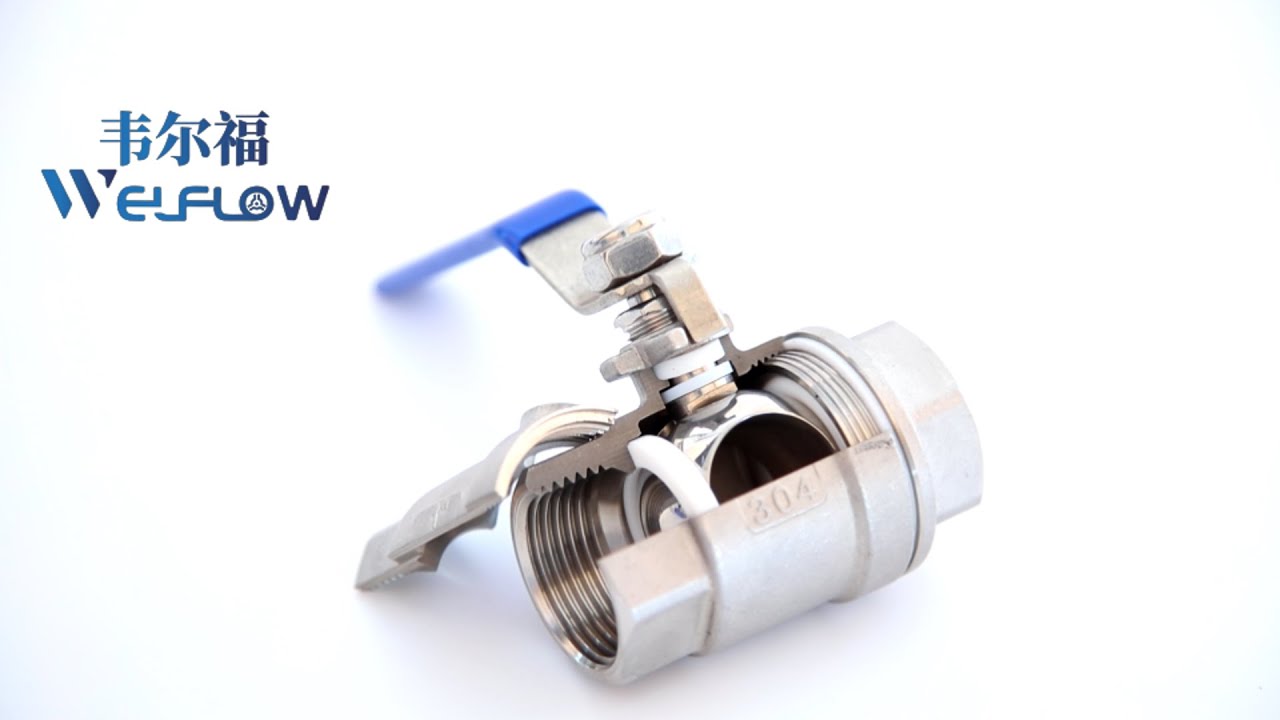
Three-Piece Ball Valve (3PC)
Three-piece ball valves are constructed with three separate pieces: a body and two end caps. The end caps are connected to the body using bolts, allowing easy disassembly and maintenance. This ball valve type offers greater flexibility for repairing or replacing internal components.
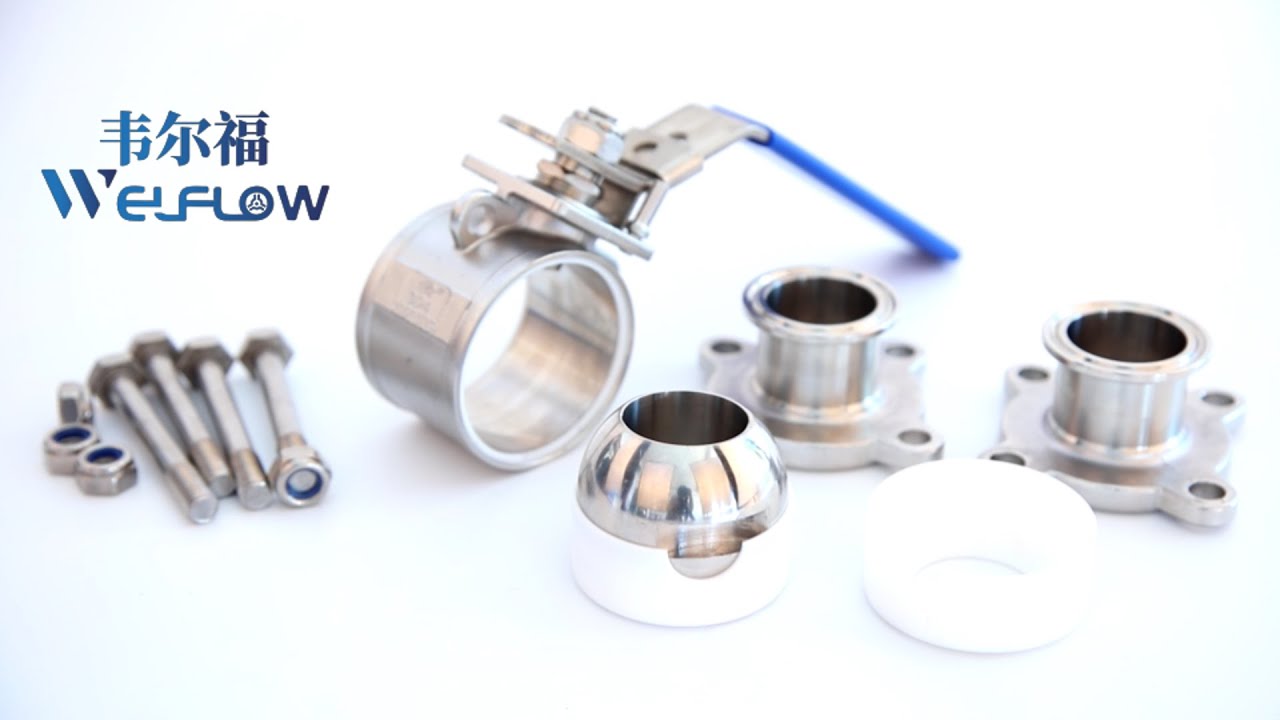
HOW BALL VALVE WORK?
Ball valves work by utilizing a rotating sphere (or “ball”) with a hole bored through the center. Here is a simple explanation of how a ball valve works:
Open Position: When the valve is in the open position, the hole in the ball is aligned with the direction of the flow path, meaning that fluid can flow through it. The handle of the valve is usually in line with the hole in this position.
Closed Position: When the valve is closed, the ball is rotated 90 degrees so that the hole is perpendicular to the flow path, meaning fluid cannot pass through. The handle is typically perpendicular to the hole in this position.
Where Are Ball Valves application
Ball valves are used in a wide variety of applications across many industries due to their reliability, durability, and ease of operation. Here are some common applications:
- Oil and Gas Industry: Ball valves are used for controlling the flow of oil and gas in pipelines and other processing equipment.
- Chemical Industry: They are used in chemical plants for controlling the flow of various chemicals in the processing lines.
Water and Wastewater Treatment: Ball valves are used in water supply systems and wastewater treatment plants for controlling the flow of water and other fluids.
Food and Beverage Industry: They are used in food processing and beverage production lines to control the flow of liquids and semi-liquids.
Pharmaceutical Industry: Ball valves are used in pharmaceutical manufacturing for controlling the flow of ingredients and finished products.
Power Generation: In power plants, ball valves are used in various systems such as cooling, lubrication, and fuel supply.
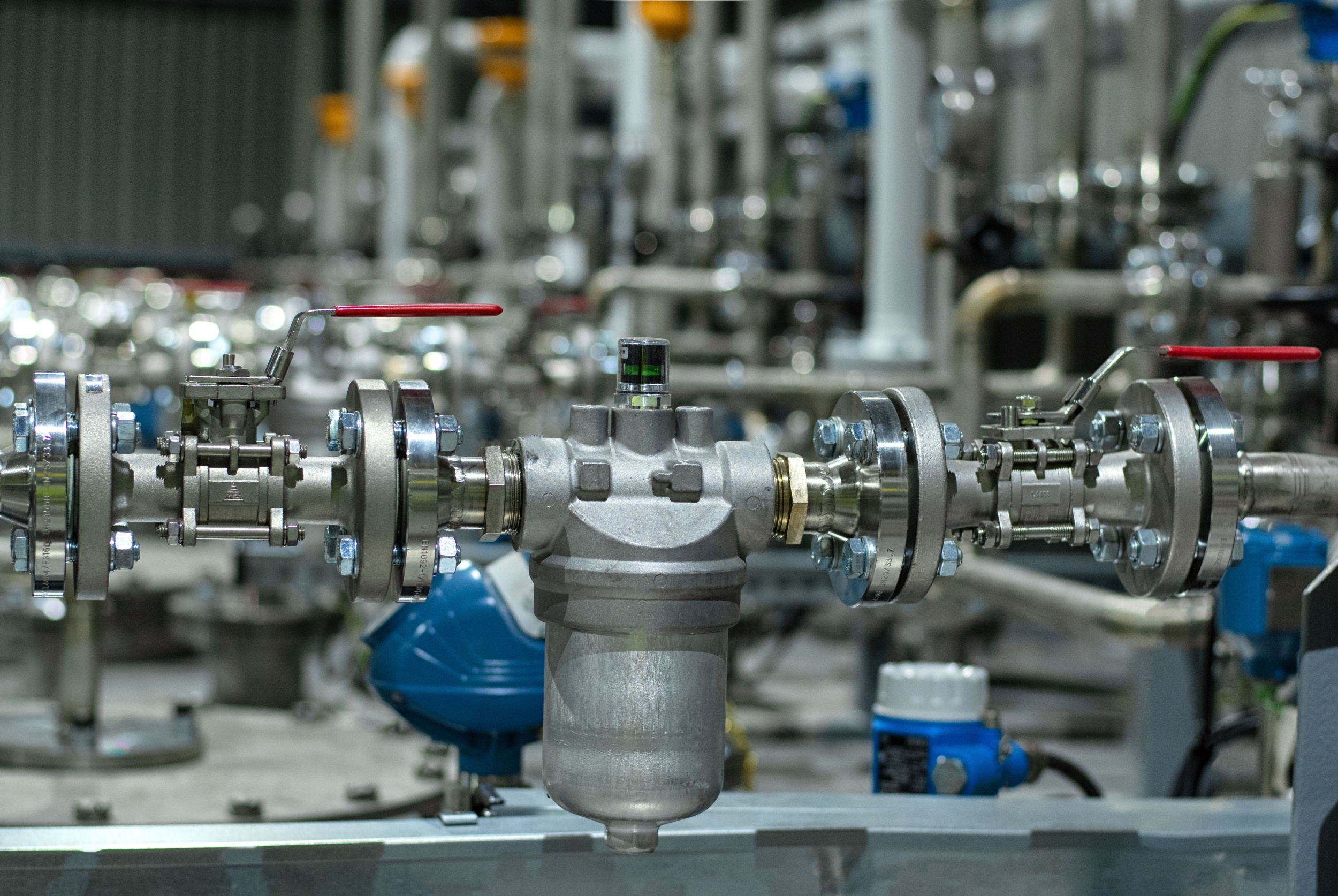
7. Marine Applications: Ball valves are used in various marine applications, including fuel systems, water systems, and waste systems on ships.
8. Residential Plumbing: In homes, ball valves are commonly used as shut-off valves in water supply lines.
Body
The body of the valve, made from stainless steel, is the outer casing and provides the main structure. It contains the internal parts and has connections (ports) for the pipeline.
Ball
The ball is the central component that controls the flow of fluid. It's a sphere with a hole through the middle, which aligns with the pipeline when the valve is open and is perpendicular to it when the valve is closed.
Stem
The stem is the part that connects the handle to the ball. When the handle is turned, the stem rotates the ball.
Seats
The seats are rings of softer material (often PTFE or another plastic) that form a seal between the ball and the body when the valve is closed. There are typically two seats, one on either side of the ball.
Seals
Seals or packing material are used to prevent leakage along the stem. They ensure that when the valve is closed, no fluid can escape.
Bonnet
The bonnet is a part of the valve body that holds the stem. It's often bolted onto the body and provides a seal to prevent leaks.
FACTORS TO CONSIDE WHEN CHOOSE BALL VALVE
1# Material
The material of the valve should be compatible with the fluid or gas it will control. Common materials include stainless steel, brass, and plastic, each suitable for different applications.
2# Type of fluid
The type of fluid that the valve will control is crucial. Different materials are suitable for different types of fluids, and the valve must be compatible with the fluid to prevent corrosion or damage.
3# pressure rating
The pressure rating of the valve should be suitable for the application. If the pressure is too high for the valve, it could fail.
4# size
The size of the valve should match the size of the pipe it will be connected to.
5# TEMPERATURE
The temperature of the fluid can also affect the performance of the valve. Some materials can withstand high temperatures, while others cannot.
7# Operation
Consider whether you need a manual or automated valve. Manual valves are operated by hand, while automated valves can be controlled remotely or programmed to open and close at certain times.
6# Seat & Packing Material
Ball valve seats are made from different materials depending on the application. Soft seats, often made from PTFE (like Teflon), are great for sealing but have limited pressure thresholds, making them suitable for low-pressure applications. Filled PTFE is used for mid-range pressure applications, while high-pressure applications use PEEK. Neoprene or fluorocarbon elastomer is used for applications resistant to oil and moderate chemicals but not for highly corrosive acids. For high-temperature applications, graphite is used due to its heat resistance. The choice of seat material depends on the pressure rating of the ball valve and the materials it will be in contact with.
8# Port
Ports, serving as the inlet and outlet points of valves, can be either full or standard. They have the ability to limit the flow of fluids or gases.
- Full Bore Ball Valve
A full bore ball valve is a valve with a hole, or port, that matches the pipe’s inside diameter. This design allows unrestricted fluid flow, minimizing pressure loss.
- Reduced Ball Valve
A reduced bore ball valve has a port smaller than the pipe’s diameter, causing some restriction to fluid flow and a potential pressure drop. They are typically smaller, lighter, and less costly than full bore valves, suitable for non-critical flow rate applications.
- V -Port Ball Valve
A V-port ball valve has a V-shaped hole in the ball, allowing precise control over flow rate. It’s ideal for applications requiring flow modulation, providing a wide range of control over the fluid or gas passing through.
HELP YOU SELECT THE RIGHT VALVES
Send us a message if you have any questions about ball valves. Our experts will give you a reply with 24 hours to help you select the right valve you want.
Tel: +86-577-88893652
Email: [email protected]